Journal Search Engine
ISSN : 2234-1099(Online)
DOI : https://doi.org/10.5000/EESK.2013.17.1.021
다지점 진동대를 이용한 원자력발전소 배관계통의 내진성능실험
Seismic Capacity Test of Nuclear Piping System using Multi-platform Shake Table
Abstract
- (3)12-26.pdf3.70MB
- 1. 서 론
- 2. 진동대 실험
- 2.1 실험 개요
- 2.2 배관실험모델의 구성
- 2.3 계측 및 가진 방법
- 3. 실험결과
- 3.1 진동대 가진 결과
- 3.2 동특성 분석
- 3.3 배관응력분석
- 4. 결 론
- / 감사의 글 /
1. 서 론
원자력발전소(이하 ‘원전’) 배관의 파괴를 발생시키는 원인 하중은 주로 관내의 유체 압력, 고정하중, 온도팽창 그리고 지진하중 등으로 알려져 있는데, 이중에서 지진하중을 제외한 여타 하중들은 원전 가동 시 배관에 항시 작용하므로 그 물리적 특성과 적절한 경계조건을 고려하면 비교적 정확하게 평가할 수 있다. 그러나 작용빈도는 작으나 하중의 크기가 상대적으로 큰 지진에 대해서는 고려해야할 하중들이 지진의 발생위치로부터 복잡한 과정을 거쳐서 전달되므로 지진하중에 의해 배관에 발생하는 응력을 정확히 예측하기 어려우며, 이로 인해 과도하게 안전 여유도를 갖도록 배관을 설계하는 경향이 있다[1]. 원전의 안전한 운영의 측면에서 이러한 여유도는 불가피한 것이나, 원전 배관계통의 적용된 설계기준과 비교하여, 실제 원전에서의 배관의 안전성 및 여유도를 평가, 분석하는 연구가 필요한 실정이다.
지진하중을 고려한 원전 배관계통의 설계 및 발생 응력에 대한 연구는 관련 산업의 발전과 함께 체계적으로 이루어져 왔으나, 대부분의 기존 연구들은 단순 배관요소에 대한 실험결과를 바탕으로 한 연구결과들이며, 실제와 같이 복잡한 거동을 나타내는 배관계통에 대한 실험을 수행하고 그 성능을 평가한 연구사례는 많지 않다.
일찍이 유압진동대가 개발되어 연구에 사용되기 시작하였으나, 초기 진동대 장비를 이용하여 복잡한 구성을 가지는 배관계통에 대한 내진 실험을 수행하기에는 어려움이 있었다. 1980년 Keowen et al.[2]은 지진 시 rigid element, mechanical shock-arrestor, triaxial visco-elastic 배관 감쇠기를 적용하여 배관의 내진성능을 확인하기 위한 실험을 유압 가력기를 이용하여 수행하였다. Multi-bends simulated motor operated valve 등의 구성요소를 고려한 총길이 15.2 m, 직경 200 mm, 150 mm의 가압된 배관을 5개의 유압 가력기에 의해 작동되는 테이블 위에 설치하여 ASME 기준에 따른 배관 응력의 변화된 수준과 적용된 지지대 형식을 기준에 따라 분석하였다.
1995년 프랑스에서는 ELSA(European Laboratory for Structural Assessment)의 진동대를 이용하여 배관요소의 지진거동분석 실험프로그램을 진행하였다[3]. 2가지 재료가 다른 배관요소에 대한 실험이 수행되었으며, 구조체의 동적거동 특히, 곡관의 거동을 중심으로 내진성능을 분석하였다. 실험결과에서는 작용하중에 의해 각 곡관에 소성변형이 발생한 것을 확인하였으며, 이러한 변형은 전체적인 배관계통의 성능 향상과 지진 시 거동 측면에는 좋은 효과를 나타냄을 확인하였다. 또한, 배관에 국부적인 소성변형이 발생하면 지진에 의한 거동이 복잡해지는 반면, 배관계통의 응답을 평가하고 지진에 의해 발생할 수 있는 손상을 방지하기 위해서는 배관의 소성거동을 이해하는 것이 필수적인 것으로 평가되었다.
비교적 대구경의 길이가 긴 배관계통에 대한 본격적인 실험적 연구가 JNES (Japan Nuclear Energy Safety)와 NUPEC (Nuclear Power Engineering Corporation)에 의해 수행되었다[4]. 다년간 다양한 배관 구조에 대한 실험적 연구를 진행하였으며, 이러한 실험은 원전배관계통의 극한강도, 탄소성응답을 보다 잘 이해하고, 배관 설계기준에서 내진 여유도를 확인함으로써 수정된 ASME 응력기준을 평가하기 위해 실시되었다. 이 연구에서는 재료실험, 요소실험, 배관계통에 대한 진동대 실험 등이 수행되었고, 재료와 형태가 다른 배관요소에 대한 정, 동적 실험을 실시하였으며, 실험결과, 지진하중으로 인한 배관요소의 손상형태는 저 진동수의 피로 파괴라는 것이 확인되었다. 배관계통의 진동대 실험 결과는 요소실험과 유사한 양상을 나타내었으나, 배관계통을 구성하는 요소 내부의 국소변형으로 인해 다른 요소부위에서 하중의 재분배가 발생하여, 계통 전체로 볼 때에는 요소실험 연구 결과보다 안전한 것으로 평가되었다. 실험된 배관의 파괴에는 설계기준 작용력과 비교하여 3배 이상의 하중이 요구되었으며, 2% 이하의 감쇠가 적용되어야 하는 것으로 판단되었다. 주요 에너지소산은 가진력이 증가함에 따라 배관에서 소성변형이 발생하는 경우에 나타났다[5].
이상의 연구들로 볼 때 전체적인 원전기술의 발전에 비하여 배관계통에 대한 동적거동이해 및 이와 관련된 연구, 특히 지진하중과 같이 큰 하중이 작용하는 경우 배관의 탄소성 거동을 이해하기 위한 실험적 연구가 미흡한 실정이며 이에 대한 연구의 필요성이 큰 것으로 나타났다. 본 연구에서는 원전 배관계통에 지진이 발생했을 시의 거동을 실제 현장에서 적용되고 있는 배관계통을 대상으로 진동대 실험을 수행하고 그 결과를 분석함으로써, 배관의 동적특성과 현재 국내 원전 배관계통에 적용되고 있는 설계기준에 대한 안전성 및 내진 여유도를 분석하였다.
2. 진동대 실험
2.1 실험 개요
본 실험의 목적은 실제 원전에서 사용되고 있는 배관요소 중 일부를 모사하여 진동대 실험을 수행하고 동적특성 및 내진성능을 분석하는 것이다. 원전 배관계통에서의 중요도와 진동대의 실험가능 면적 등을 고려하여 실험체를 제작하였다. 이를 위해 실제 건설 중인 원전을 방문하여 현장조사를 실시하였으며, 그 결과 Fig. 1과 같은 목표배관계통을 선정하였다. 선정된 배관계통은 냉각계통의 부족한 수량을 공급하는 역할을 맡고 있다.
Fig. 1. Tested nuclear piping system drawing(ISO) and photos
배관은 ASME Class 1 SA312 Grade TP316 Sch. 160으로 분류되는 스테인리스 재질의 공칭직경 60.3 mm (2in.)와 88.9 mm (3 in.) 배관으로서 직관, 곡관, 변단면관을 갖고 있으며, 서포트, 지지대 등 다양한 요소들로 구성되어 있다. 격납건물 내부에 설치된 배관은 높이 약 31.0 m ~ 34.7 m인 2개 층에 걸쳐 연결되어 있다. 높이 31.0 m에 위치한 배관계통의 하단부에서 주냉각계통과 용접으로 연결되어 있으며, 다수의 곡관 결합을 이용하여 수직으로 방향을 전환한 후 상단부에서 일정한 높이를 유지하여 공급계통과 연결되는 구조이다.
선정된 배관계통은 다양한 형태의 서포트와 지지대(Fig. 1의 Photo 참조)에 의해 지지되어 있으며, 지지점 경계부의 높이는 각 층의 바닥 및 천정으로 한정되는 것으로 조사되었다. 지진 시 배관에 전달되는 힘은 격납건물 내부에서 이러한 지지점이 위치하는 높이의 증폭된 응답을 고려해야 할 것으로 판단되었다. 본 연구에서는 부산대학교 지진방재연구센터에 설치된 2기의 진동대[6]를 이용하였으며, 실험배관계통의 하단부와 상단부를 각기 다른 진동대에 연결하여 격납건물 내에서 높은 위치에 설치된 배관 지지부에 보다 큰 가속도가 발생하는 것을 모사할 수 있도록 계획하였다.
Photo 1. Overview of shaking table test
Photo 2. SUPPORT 3 and DDVS target
2.2 배관실험모델의 구성
배관실험체 설치도면을 Fig. 2에 나타내었으며, 설치 후 전경을 Photo 1, 2에 나타내었다. 배관실험체의 전체 길이는 21.2 m이고 7개의 곡관과 양단부에 2개의 변단면관이 적용된 형태이다.
2개의 진동대 위에 실제 경계조건을 모사할 수 있는 강재기둥(Fig. 2 참조)을 조립한 후 배관을 용접하여 연결하였다. 격납건물 내에서 선정된 배관 지지점의 해당 높이를 모사하기 위한 총 3개의 강재기둥(Fig. 3 참조)을 좌측 진동대에 2기, 우측 진동대에 1기 설치하여 고정단 연결부(Fig. 2의 FIX 1, 2), 행거서포트(Fig. 2의 HANGER 1, 2), 단순지지대(Photo 2 참조)를 설치할 수 있도록 하였다. 자중에 의한 처짐을 최소화하고 조립 시 비틀림을 방지하기 위하여 전체 배관을 바닥에서 용접하여 완성한 후에 크레인으로 인양하여 진동대 위에 설치하고 양단 경계부를 최종 용접하는 순서로 조립하였다. 모든 배관 부품 및 구성요소는 ASME Boiler and Pressure Vessel Code[7]에 준하여 설치, 조립하였으며, 실험 시 관의 내부는 상온의 물로 만관되어 20 MPa로 가압된 상태였다. 실험체의 조립 및 설치과정을 Photo 3에 나타내었다.
Fig. 2. Piping specimen details (sensor location and orientation)
Fig. 3. Support details for boundary conditions
Photo 3. Piping specimen assembling
진동대 상부에서 각 지지점이 설치된 위치는 실제 원전 현장에서 지지점이 설치된 위치를 유사하게 적용하였으나 2기의 진동대 사이의 공간(Fig. 2참조)에는 경계조건을 만족시키기 위한 프레임 설치가 곤란하였다. 따라서 실제 설계에서 반영되어야하는 2기의 행거서포트가 설치되지 못 하였으므로 이 구간에서는 보다 큰 응력이 발생할 것으로 예측되었다.
2.3 계측 및 가진 방법
배관의 동적거동을 확인하고 가진력에 의한 각 배관요소, 특히 곡관부의 발생응력을 조사하기 위하여 Fig. 2에 나타낸 것과 같이 가속도계와 변위계, 변형률계를 설치하였다.
유연한 배관 실험체의 가속도 응답과 고유진동수, 감쇠를 확인하기 위하여 저 진동수 대역(0.1~180 Hz)에서 계측능력이 우수한 10g 용량의 Kistler사 8305B10 MEMS 형식 단축 가속도계 6개(Fig. 2의 AM1~6)를 설치하였다. 가속도계의 설치위치 및 방향은 배관의 종방향(X) 및 횡방향(Y)의 동적 응답을 계측할 수 있도록 결정되었다. 또한, 강재기 둥의 가속도 증폭 및 응답특성을 조사하기 위하여 최대 10g 가속도 계측이 가능한 PCB사 603C11/010AC 단축 가속도계 6개(Fig. 2의 AI1~6)를 설치하였다. 강재기둥에 적용된 PCB사의 제품은 일반적으로 기계진동측정(1~5,000 Hz)에 주로 사용되는 것으로 강성이 큰 강재기둥의 응답을 조사하는데 적합하다고 판단하였다. 가속도계를 소정의 위치에서 배관의 종방향과 횡방향으로 각각 설치하였다.
진동대에서 발생된 가속도를 확인하기 위하여 진동대 자체 제어용으로 설치된 가속도계의 피드백 신호를 활용하였다. 중요 배관요소에 발생하는 응력을 확인하기 위하여 Tokyo Sokki Kenkyujo사의 YFLA-5-11 변형률계(Strain gage)를 Fig. 4(A)와 같이 변단면관과 곡관부(Fig. 2의 ELBOW 및 FIX 위치)에 설치하였다. 특히, 응력이 크게 발생할 것으로 예측되는 곡관부의 내, 외호면과 양측 중립위치에서의 배관의 길이방향 변형률이 계측될 수 있도록 설치하였다.
Fig. 4. Stain gauge location(orientation) and DDVS Target
원형단면의 배관이기 때문에 기존의 동적실험 연구에서 일반적으로 사용되는 접촉식 변위측정방법을 적용하여 변위를 계측하는 것이 어려울 것으로 판단되었다. 이에 본 연구에서는 변위측정을 위하여 동영상 촬영에 의한 간접변위 측정방법인 DDVS[8](Dynamic Displacement Vision System)를 활용하였다. DDVS는 초당 60프레임을 촬영할 수 있는 디지털 캠코더를 이용하여 설치된 타깃의 변위를 측정하는 기술로, 촬영된 평면의 X축(타깃의 좌우 방향) 및 Y축(타깃의 상하 방향)의 변위를 동시에 측정하는 것이 가능하다. DDVS에 의한 계측은 촬영 가능 프레임수의 제한으로 측정가능 진동수에 한계가 있으나, 본 실험에서의 배관 구조물 거동을 분석하기에는 충분할 것으로 판단되었다. 총 8개의 타깃이 설치되었으며, 설치된 DDVS 타깃의 규격은 Fig. 4(B)와 같고 설치 전경은 Photo 2와 같다.
가속도 및 변형률 데이터의 획득을 위하여 National Instrument사의 264채널 DAQ(Data acquisition) 시스템을 이용하였다. 이 시스템은 진동대 피드백 신호와 실시간으로 연동돼있어 진동대에서 발생하는 변위 및 가속도를 동시에 기록하는 것이 가능하다. 계측 샘플링 속도는 256 Hz 이며, 계측 시 하드웨어적인 필터링은 적용되지 않았다.
진동대 장비는 MTS Systems사 600kN 용량 3자유도 진동대(Photo 1의 좌측상부)와 300kN 용량의 6자유도 진동대(Photo 1의 우측하부) 2기이며, 각 진동대를 동시에 제어하기 위하여 장비 개발사의 STEX[9] (Seismic Test Execution) 프로그램이 사용되었다. 또한 진동대에 강재 기둥만을 설치한 상태에서 동시 가진 성능을 확인(Iteration)한 후 실험체를 설치하였다.
Table 1은 실험 가진표로서 입력지진파, 가진 방향 등을 나타낸 것이다. 진동대의 가진은 2대의 진동대에 동일한 지진파를 입력하여 가진한 경우와, 높이가 다른 지지점 설치에 따른 격납건물의 증폭된 응답을 반영하기 위해 좌측 진동대(Fig. 2의 Table B)에 가진력을 증가시킨 다지점 가진의 경우로 구분하였다. 또한, 가진 방향에 따른 영향을 분석하기위하여 설치된 배관의 종방향과 횡방향으로 가진 한 후 종, 횡방향에 대하여 동시 가진을 실시하였다.
Table 1. Tested excitation cases
상기 경우에 대하여 제작된 인공지진파의 최대 가속도를 기준으로 100%에서 500%까지 단계별로 진동대 가진 수준을 점증시켰다. 각 지진파 가진 실험 전과 후에는 실험체의 고유진동수를 분석하고 상태 변화를 확인하기 위하여 0.5 ~ 50 Hz의 진동수 성분을 가진 백색파 (White noise)를 RMS (Root Mean Square)값이 0.1 g가 되도록 입력하여 가진하였다. Fig. 2의 좌측 진동대는 수평방향 가진만 가능하도록 설계되었기 때문에 수직방향 가진의 경우는 본 연구에서 고려되지 못 하였다.
진동대 실험의 가진 수준을 격납건물에 적용되는 수평방향의 층응답스펙트럼을 요구응답스펙트럼(RRS, Required Response Spectrum) 으로 규정하고 P-CARES 2.0[10], 프로그램에 의해 작성된 가속도 시간이력을 인공지진파로 사용하였다. NS(X), EW(Y) 방향으로 각각 작성된 지진파는 ASCE 4-98[11,12]을 참고하여 강진 지속시간은 10초, 총 가진 시간은 18초로 작성되었다. 각 방향 인공지진파의 시간 이력과 5% 감쇠를 고려한 요구응답스펙트럼 및 실험응답스펙트럼(TRS, Test Response Spectrum)을 Fig. 5에 나타내었다.
Fig. 5. Shake table acceleration time history and response spectra (M8)
다지점 가진의 경우는 우측 진동대에 비하여 10% 증폭된 가속도 신호를 좌측 진동대에 입력하여 동시 가진함으로써 지지점 높이에 따른 구조물의 가속도 응답차이가 배관에 작용하는 가속도로 반영되도록 하였다. 이러한 설정은 선정된 배관이 설치된 위치가 격납건물 내에서 동일한 평면에 위치하고 경계부의 높이만 다르기 때문에 두 지점 간에 위상 차이는 크지 않을 것으로 판단하였기 때문이다. 또한, 각 지지점 설치 위치에서의 가속도 응답을 실제 원전에서 격납건물 내부의 설치조건을 모두 고려한 상세해석을 수행한 후 결정하는 것이 보다 실제와 유사한 결과를 얻을 수 있으나, 본 연구에서는 지지되는 층의 높이 차이에 의한 상대적인 가속도비를 10%로 가정하여 실험하였다.
3. 실험결과
3.1 진동대 가진 결과
본 실험은 비교적 길이가 긴 배관실험체를 대형 진동대 2기에 분산 설치한 후 동시에 가진하여 배관의 동특성 및 내진성능을 확인하는 실험이므로, 가진 결과로부터 RRS를 만족하는 수준의 가진이 이루어졌는지에 대한 확인과 실험장비의 동시 가진 성능을 분석하였다.
Fig. 6은 M5 실험 시 각 진동대 상부에서 계측된 가속도와 변위의 시간 이력을 나타낸 것이고, Fig. 7은 최대 가진인 M28 실험의 진동대 변위시간 이력을 나타낸 것이다. 각 신호간의 시간지연 및 위상차는 발생하지 않았으며, 최대 변위 및 가속도의 차이는 크지 않은 것으로 나타나 두 진동대는 동일한 운동을 한 것으로 판단할 수 있었다. 또한 Fig. 7에서와 같이 다지점 가진의 경우에서도 정밀한 제어가 가능한 것을 확인하였다.
Fig. 6. Comparison of table displacement and acceleration feedback between shake table B and C (M5)
Fig. 7. Shake table displacement feedback (M28)
Fig. 8은 본 연구에서 설정한 가속도 RRS와 M6 ~ M8 실험 시 각 진동대에서 계측된 가속도 TRS를 비교한 것이다. 가진 결과는 대부분 RRS를 만족하는 수준이었으나 X방향의 경우 15 Hz, Y방향은 20 Hz 이후 구간에서 요구한 수준보다 비교적 큰 가속응답이 일부 계측되었다. 이것은 경계조건을 모사하기 위하여 설치된 강재기둥의 공진에 의한 영향으로 판단되었는데, 일반적으로 본 실험에서 사용된 것과 같은 대형의 유압진동대의 경우, 설치된 실험체, 구조물 등의 공진에 의해 제어기능이 영향을 받을 수 있다.
Fig. 8. Tested acceleration response spectra of M6, M7, M8
Fig. 9는 백색파 가진 실험(M1, M2) 시 각 강재기둥의 공진점을 AI 가속도계에 대한 진동대의 가속도 계측결과의 전달함수[14]를 산출하는 방법을 통해 분석한 것으로, SUPPORT 2의 경우 X방향으로 15.62 Hz, Y방향으로 29.57 Hz, SUPPORT 1의 경우, Y방향으로 28.93 Hz에 공진점을 갖고 있는 것을 확인할 수 있었다. 그러나 이러한 높은 진동수를 갖는 공진에 의한 영향은, 비교적 낮은 진동수를 갖는 배관 실험체의 전체적인 거동에 큰 영향을 미치지 않을 것으로 판단하여 실험을 진행하였다.
Fig. 9. Natural frequency estimation of steel frame support
3.2 동특성 분석
배관실험체의 진동 특성을 파악하기 위하여 고유진동수와 감쇠비 및 가속도, 변위 응답 특성을 분석하였다. 일반적으로 진동실험에서 기록된 계측 신호에는 가진의 여러 원인에 의하여 오차가 포함되며, 기준선의 왜곡이나 편향 등이 발생할 수 있어 기준선보정 및 필터링 등의 신호처리 과정이 필요하다[13]. 본 연구에서는 대부분의 가진 진동수 영역이 포함되는 30 Hz 이하의 구간에 저역통과필터를 사용하여 이상 신호 및 왜곡현상을 제거한 후 분석하였다.
고유진동수는 진동대에서 계측된 가속도 신호를 입력으로 하고 배관에 설치된 AM 가속도계들의 계측신호를 출력으로 하여 전달함수[14]를 산정하는 방법으로 측정하였다. 2기의 진동대에 의해서 가진되었기 때문에 입력신호 2개가 존재하지만, 3.1절에서 언급한 것과 같이 2기의 진동대가 동일한 운동을 한 것으로 가정하고 좌측 진동대의 가속도 신호를 입력신호로 사용하여 전달함수를 산정하였다.
실험 초기(M1, M2) 및 최종(M23, M24)단계에서 실시된 백색파 가진 실험 시 각 AM 가속도계 위치에서 X, Y방향의 전달함수는 Fig. 10과 같으며, 가속도 응답비(입력가속도에 대한 응답가속도의 비)가 2 이상인 진동수를 고유진동수로 규정하여 추정한 결과는 Table 2와 같다. Fig. 10에서 최종단계의 가속도 응답비가 초기 단계보다 크게 나타나는 것은 최종 가진 시의 백색파 가진 시간이 2배 정도 길었기 때문에 각 첨두 가속도 응답비가 증가한 것이다. 실험 초기 및 최종단계의 추정결과 차이는 최대 7% 정도로 유사한 결과를 나타내어 최대 가진 이후에도 배관의 구조적 이상은 발생하지 않은 것으로 판단할 수 있었다.
Fig. 10. Transfer function estimation results of the specimen
Table 2. Natural frequency estimation results
전달함수 산정결과를 보면 다양한 모드들이 존재함을 알 수 있으나, 본연구에서는 이러한 모드형상을 추정하는데 한계가 있었다. 가속도계의 수량이 모드형상을 분석할 수 있을 정도로 충분하지 못하였고 수직방향 가속도계 또한 설치되어 있지 않았다. 이것은 실험준비단계에서 가속도계 위치 및 방향의 선정을 수평방향의 가속도 응답의 크기를 측정하기 위한 용도로 계획하였기 때문이다. 모드형상은 추후 해석적 연구를 통하여 보완할 예정이다.
일반적으로 진동대 실험에 의한 실험체의 감쇠 추정에는 대수감소율법, 1/2파워밴드폭법 및 곡선접합법이 주로 사용된다. 이 중 1/2파워밴드폭법 및 곡선접합법은 시스템이 단일모드에 지배적인 경우에 매우 효과적인 방법이나 본 실험에서와 같이 다양한 모드가 존재하는 경우에는 적용이 쉽지 않다. 특히, 곡선접합법의 경우 전달함수를 다항식으로 전개하여 각 계수를 결정함으로써 고유진동수와 감쇠 특성을 추정할 수 있는데, 이 계수의 산정시 모드특성이 복잡한 경우에는 오차가 크게 발생할 수 있다. 본 연구에서는 이러한 점을 감안하여 대수감소율법을 이용하여 감쇠를 추정하였다.
대수감소율법에 의한 감쇠비 산정에는 실험체의 자유진동으로부터 신호의 감소량을 측정하는 것이 필요하다. 그러나 본 연구에서는 이러한 자유진동을 발생시키기 위한 실험을 추가적으로 수행하지 않았기 때문에 저차모드가 지배적인 Y방향 가진이 종료된 후 측정된 가속도 신호를 변위로 환산한 것을 자유진동신호로 이용하여 감쇠비를 산정하였다. M3부터 M27 가진 시까지의 감쇠비는 Table 3과 같으며, 각 신호의 회귀분석결과는 Fig. 11과 같다.
Table 3. Damping estimation results
Fig. 11. Decay curves for Y-dir. damping calculation
감쇠비는 3.13 ~ 4.98 %로 분포하는 것으로 나타났으며, 가진력의 차이가 크지 않았던 M14 가진까지의 감쇠비는 비슷한 수준이었으나, 이후 가진력이 증가함에 따라 감쇠비도 증가하는 양상을 나타내었다. 다만, 본 연구의 실험에서는 일부 생략된 행거서포트의 구속효과 및 가진 횟수 증가에 의해서 일부 계측되지 못한 지점에서 손상 등이 발생하였을 수 있으므로 일반화하여 단정하기는 곤란하다. 또한, 감쇠비 결정을 위하여 선정한 자유진동구간의 시작점, 즉 정확한 가진 종료 시점을 확인하기 어렵기 때문에 산정된 감쇠비에 다소 오차가 포함되었을 수 있음을 참고해야 한다.
Fig. 12는 가진 수준에 따른 Y방향 계측가속도를 나타낸 것이다. 지지부의 입력 가속도가 증가할수록 실험체의 응답가속도 역시 선형적으로 증가하였으나, Fig. 13에 나타낸 것과 같이 각 단계에서 측정된 최대 가속도를 입력 최대 가속도의 비로 나눈 응답 비를 산정한 결과는 약 40% 이하이었다. 이러한 결과는 X, Y방향을 동시 가진한 경우(Fig. 14, 15 참조)에서도 동일하게 나타났으나 X방향 보다는 Y방향의 가속도 응답이 더 크게 발생하였으며, 양방향 가진의 경우 Y방향에서는 가진력이 증가할수록 가속도 응답의 비가 감소하는 경향을 나타내었다. 이러한 점은 배관구조 Y방향의 1차 모드진동수가 주요 가진 진동수 대역보다 낮은 약 2 Hz이었기 때문인 것으로 판단된다.
Fig. 12. Acceleration response comparison for Y direction
Fig. 13. Acceleration response ratios for Y direction
Fig. 14. Acceleration response comparison for X-Y direction
Fig. 15. Acceleration response ratios for X-Y direction
Table 4는 각 방향 및 가진 수준별 실험체의 최대 응답 가속도를 나타낸 것이다. X방향 및 다지점 양방향 가진에 대한경우가 100% 및 150%로 제한적이기 때문에 비교 대상이 많지 않으나 양방향 가진 및 다지점 가진에 의한 영향은 크지 않은 것으로 판단된다. 특히, 다지점 가진은 좌측 진동대에 가진력이 증가하여 가력되었음에도 길이가 길고 유연한 배관구조의 특성에 의해 전체 구조에 미치는 영향은 크지 않은 것으로 판단된다.
Table 4. Maximum accelerations by excitation direction
Fig. 16은 Y방향 가진 시 DDVS에 의해 계측된 변위 측정결과를 요약한 것이다. 가속도 측정결과와 같이 가진력이 증가할수록 최대변위응답이 선형적으로 증가하는 양상을 나타내었다. DDVS에 의한 변위측정은 영상촬영 기법의 특성상 타깃의 전후 방향의 변위를 측정하기 어려우며, 측정대상의 속도가 빠른 경우 측정이 어려운 단점이 있다[8]. 본 실험의 결과에도 이러한 이유로 다소 결과가 제한적이다.
Fig. 16. Displacement measurement results
3.3 배관응력분석
최종 가진까지 배관의 균열 및 파괴, 단면의 변형 등은 발생하지 않았다. Table 5와 Fig. 17은 가진 수준별 측정된 변형률을 나타낸 것으로, 가진 수준이 증가할수록 발생 변형률이 증가하는 것으로 나타났으며 ELBOW 5의 중립위치에서 최대 변형률이 발생하였다. 최대 변형률은 진동대 실험 전수행한 배관요소 및 재료의 정적실험결과[16]와 비교하여 매우 낮은 수준으로서 배관은 탄성 상태임을 알 수 있다.
Table 5. Maximum strain by excitation method
Fig. 17. Measured strain comparison result
변형률 측정결과에서는 가속도 측정결과와 달리 다지점 가진에 의하여 보다 큰 변형률이 발생한 것으로 나타났는데, ELBOW 5 위치에서 배관의 상하방향 운동에 의한 곡관부 중립축에 응력이 크게 발생하였기 때문인 것으로 추정된다. 실제 배관이 위치하고 있는 격납건물의 동일 평면상에서 높이 차이만 있는 위치의 구조물 응답이 본 실험에서 적용한 것과 같이 선형적이라고 가정한다면, 다지점 가진을 고려하는 경우 배관에 보다 큰 응력이 작용할 수 있는 조건임을 알 수 있다. 그러나 다지점 가진에 의한 영향은 가진력이 200%인 경우로 한정된 결과이므로 일반화에 제한이 있다. 이러한 점은 향후 해석적 연구를 통하여 확인할 필요가 있다.
상기와 같이 측정된 변형률에 설계탄성계수 205 GPa을 적용한 발생응력을 설계기준응력 수준과 비교하였다. 본 연구에서 사용된 배관은 극한하중 작용 시 ASME Section Ⅲ, Division Ⅰ, Subsection NB의 적용이 가능하며, 여기서 제한하고 있는 응력 기준은 식 (1), (2)와 같다.
여기서, P = 관내부의 작용 압력(MPa), D0 = 외경(mm), t = 관두께(mm) , I = 단면2차모멘트(mm4), ME = 자중효과를 고려한 발생모멘트(N·mm), B1, B2, B2′= 주응력지수, Sm = 배관허용응력(MPa) 이며, B1, B2는 ASME Section.Ⅲ Table NB-3681(a)-1과 NB-3683.7에 의한 직관과 곡관의 주응력지수로 Table 6과 같다. 기준에 의해서 지진하중을 포함한 역학적인 하중 작용에 의한 배관의 허용응력은 2.5Sm이며, 여기서 Sm은 138MPa로 규정되어 있다.
Table 6. Primary stress index
진동대의 양방향 최대 가진 시 ELBOW 5에서 발생한 모멘트 및 응력(Sa)은 Table 7과 같이 계산되어진다. 계산된 응력의 여유도(안전율)는 2.49로서 설정한 요구응답스펙트럼의 5배 수준으로 가진하였고, 지지점의 부재로 인하여 행거서포트 2기가 설치되지 않은 점을 감안한다면, ASME에 의한 설계는 상당히 보수적인 결과를 나타냄을 알 수 있다.
Table 7. Stress calculation results of ELBOW 5
4. 결 론
본 연구에서는 실제 원전 구조물에 적용되고 있는 배관계통의 일부를 모사한 실험체에 대하여 2기의 대형 진동대를 동시에 사용하는 수평가진 실험을 수행하였으며, 배관의 동특성 실험결과 및 발생 응력에 대한 분석을 수행하여 다음과 같은 결론을 얻을 수 있었다.
1) 본 연구에서는 기존의 연구와 달리 2기의 진동대를 동시에 이용하여 전체 길이 21.2 m의 배관실험체에 대한 동적실험을 수행하였으며, 종방향, 횡방향, 양방향 및 다지점으로 가진하였다. 실험 시 2기의 진동대는 시간지연 및 위상차 없이 동일한 운동을 한 것으로 나타났으며, 상부에 설치된 실험체 및 강재기둥에 의해 진동대 제어 기능에 일부 영향이 있었으나 전체적으로 정밀한 제어가 수행된 것으로 판단된다.
2) 백색파 가진 실험의 진동대 가속도 피드백 신호와 실험체에서 계측된 가속도 사이의 전달함수를 추정하는 방법으로 배관 실험체의 고유진동수를 산정한 결과, 실험 초기 및 최종 단계의 고유진동수 차이는 최대 7% 정도로 유사한 결과를 나타내어 배관의 큰 구조적 이상은 발생하지 않은 것으로 판단되었다. 대수감소율법에 의한 감쇠비를 추정한 결과 3.13 ~ 4.98 % 로 나타났다. 가진력이 증가함에 따라 감쇠비도 증가하는 양상을 나타내었다. 그러나 본 연구의 실험에서 일부 생략된 행거서 포트의 구속효과 및 가진 횟수 증가에 의한 일부 재료의 손상 등이 발생하였을 수 있으므로 단정하기 어렵다.
4) 가진 수준이 증가함에 따라 실험체의 가속도 응답도 선형적으로 증가하는 것으로 나타났으나, 전체 실험에서 측정된 최대 가속도를 입력 최대가속도의 비로 나눈 응답 비를 산정한 결과는 최대 40% 이하로 나타났다. 이러한 결과는 배관 구조 길이의 직각방향의 고유진동수가 주요 가진 진동수 대역보다 낮은 2 Hz 이었기 때문으로 판단된다. 가속도 측정결과에서는 각 방향별 및 다지점 가진의 영향은 확인하기 어려웠다.
5) 최종 가진까지 배관의 균열 및 파괴, 단면의 변형 등은 발생하지 않았다. 가진력이 증가할수록 발생 변형률이 증가하는 것으로 나타났으며, 측정된 최대 변형률은 사전 연구에서 수행된 배관요소 및 재료의 정적실험결과와 비교하여 매우 낮은 수준으로, 배관은 탄성 상태인 것으로 판단된다. 변형률 측정결과로부터는 다지점 가진에 의해 보다 큰 응력이 발생됨을 확인하였으나, 배관의 실제 구성 조건과 비교하여 일부 요소들이 설치되지 않은 상태로 실험한 결과이기 때문에 향후 해석적 연구를 통하여 다지점 가진에 따른 배관의 거동 특성을 확인할 필요성이 있다.
6) 본 연구의 배관실험체에 발생한 응력을 ASME 설계기준응력 수준과 비교한 결과, 진동대의 양방향 가진시 최대 2.49배의 여유도를 확보하고 있는 것으로 판단된다. 이 경우의 가진력이 요구응답스펙트럼의 5배 였으며, 실제 설치 조건과 비교하여 지지점의 일부가 생략된 상태에서 나타난 결과임을 감안하면 ASME에 의한 설계는 상당히 보수적인 결과를 나타내는 것으로 판단된다.
/ 감사의 글 /
본 연구는 2011년도 교육과학기술부의 재원으로 한국연구재단의 지원을 받아 수행된 연구(No.20110001901)이고 본 연구의 저자 일부는 2단계 BK21 사업의 지원을 받았음.
Reference

2. Keowen RS, Laske A, Johnson, Merz KL. Differences in dynamic response of typical class II piping due to restraint method and input amplitude. Nuclear Engineering and Design. 1988;107:215-226.

3. Touboul F, Sollogoub P, Blay N. Seismic behaviour of piping systems with and without detect : experimental and numerical evaluations. Nuclear Engineering and Design. 1999;192:243-260.

4. Zhang T, Brust FW, Shim DJ, Wikowski G, Nie J, Hofmayer C. Analysis of JNES Seismic Tests on Degraded Piping. NUREG/CR-7015, BNL-NUREG -91346-2010.
5. Park Y, DeGrassi G, Hofmayer C, Bezler P. Analysis of nuclear piping system seismic tests with conventional and energy absorbing supports. 14th International Conference on Structural Mechanics in Reactor Technology (SMiRT 14), Lyon, France. 2008.
6. Cheung JH, Kim NS, Kim IT, Choi HS, Park CY, “KOCED Seismic Simulation Test Center” Journal of the Korean Society of Civil Engineers , 2009.Aug, Vol 57, No. 8, 43-49.
7. ASME B, Pressure Vessel Code SectionⅪ. American Society of Mechanical Engineer. 2007
8. Choi HS, Cheung JH, Kim SH, Ahn JH. Structural Dynamic Displacement Vision System using Digital Image Processing. NDT & E International. 2011 Jun;44(7):597-608.

9. MTS STEX Manual. University at Buffalo Job No. US1.17858, EQT.
10. DeGrassi G, Nie J, Hofmayer C. Seismic Analysis of Large-Scale Piping Systems for the JNES-NUPEC Ultimate Strength Piping Test Program. NUREG/CR-6983, BNL-NUREG-81548-2008
11. ASCE Standard. Seismic Analysis of Safety-Related Nuclear Structure and Commentary. ASCE 4-98. American Society of civil Engineers. 1999.
12. ASCE. Seismic Analysis of Safety-Related Nuclear Structures and Commentary. ASCE Standard 4-98, 1999.
13. Cho SG, Kim DK, GO SH. Effects of Excitation Level on the Dynamic Characteristics of Electrical Cabinets of Nuclear Power Plants. Journal of the Earthquake Engineering society of Korea. 2010 Jun;14(3):23-30.
14. Cho SG, So GH. Analysis of Ecperimental Modal properties of an Electric Cabinet via a Forced Vibration Test using a shaker. Journal of the Earthquake Engineering society of Korea. 2011 Dec;15(6):11-18.
15. ASME CODE Section Ⅲ, DivisionⅠ, Subsection NB. ASME standard. 2007.
16. Chio SJ, Seo YD, Choi HS, Kim IT, Cheung JH. Loading Experiments of the damaged TP 316 Stainless Pipe. KSCE Conference of the Civil Engineering society of Korea. 2011:69-72.
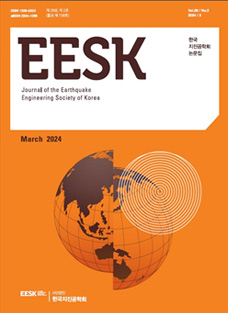
Frequency Bimonthly
Doi Prefix 10.5000/EESK
Year of Launching 1997
Publisher Earthquake Engineering Society of Korea



Online Submission
submission.eesk-j.or.kr
EESK
Earthquake Engineering Society of Korea